Letzten Sommer, exakt am 20.06.2021 veröffentlichten wir ein Interview mit Herrn Dipl.-Wirtsch.Ing. Uwe Ahrens, dem Vorstand der Altech Advanced Materials AG. Seitdem ist einiges passiert bei der Altech Advanced Materials (ISIN: DE000A2LQUJ6) und wir freuen uns, dass es nenneswerte Fortschritte bei diesem Microcap gibt, der bisher seine Ankündigungen umgesetzt hat. Es ist natürlich immer noch ein weiter Weg für das Unternehmen. Aber die ersten Schritte sind erfolgt.
Die Elektromobilität ist nun schon seit längerer Zeit einer der Megatrends an der Börse. Kein Wunder, gehen doch die Marktstudien unverändert von hohen Wachstumsraten in den kommenden Jahren und deutlichen Marktanteilsgewinnen gegenüber Verbrennern aus. Mit im Fokus ist dabei die Batterietechnologie, werden doch die Reichweite und die Lebensdauer der Batterien weiter als kritische Faktoren für die Massentauglichkeit gesehen. Gerade hier setzt die Altech Advanced Materials an . Durch eine Nanobeschichtung der Batterie-Anode mit hochreinem Aluminiumoxid soll der Erstladeverlust von ca. 8 % vermieden und zudem die Lebensdauer der Batterie um bis zu 30 % verlängert werden.
Vorab nochmals ein wichtiger Hinweis, wie beim letzten Interview. Zu beachten ist: Die Gesellschaft ist „nur“ zu 25 % an der exkluisven Technologie-Anwenderin nur für die Europäische Union beteiligt. Und wir reden von keiner bestehenden Produktion. Es geht erstmal nur um eine „potentielle“ Produktionsstätte – wobei man mittlerweile das Grundstück nach eigener Aussage erworben hat. Und die angesprochenen Patente müssen „erst noch angemeldet werden“. Herr Ahrens steht also für einen MicroCap am Anfang. Es gibt noch keine Umsätze. Noch keine Patente. Also ein hochriskantes Unternehmen. Aber wohl Fortschritte, die interessant zu sein scheinen. Wir empfehlen nach dem aktuellen Interview nochmals die Aussagen vom Juni zu lesen – spannende Entwicklung.
Herr Ahrens, bevor wir auf die neusten Entwicklungen bei Altech Advanced Materials eingehen, können Sie unseren Lesern in wenigen Worten beschreiben, was das Unternehmen macht?
Unser Ziel ist es, durch die Optimierung der Leistungsfähigkeit von Batterien einen signifikanten Beitrag zur Energiewende und Elektromobilität beizutragen. Dazu entwickeln wir aktuell ein Anodenmaterial für Batterien, das im ersten Schritt die Leistungsfähigkeit um 8 bis 10 Prozent steigert und die Lebensdauer der Zelle um bis zu 30 Prozent verlängert. Dazu beschichten wir das herkömmliche Graphit, aus dem die Anode besteht, mit einer hauchdünnen Schicht aus Aluminiumoxyd (HPA). Der Vorteil liegt darin, dass das bisher benutzte Material einfach gegen unsere Lösung ausgetauscht werden kann, ohne die Batterie in ihrem Aufbau zu verändern oder weitere Komponenten zu verändern.
Seit unserem letzten Gespräch ist nun ein halbes Jahr vergangen; was hat sich seitdem bei Altech Advanced Materials getan?
Oh, einiges. Wir konnten unsere guten und erfolgreichen Laborergebnisse, die wir bei Graphit erzielten, nun auch bei Silizium anwenden. Vor allem konnten wir richtungsweisende Leistungssteigerungen von 30 Prozent bei Lithium-Ionen-Batterien mit Hilfe unserer Technologie erzielen. Unser Technologiepartner, Altech Chemicals Limited in Australien, hat im Forschungsverfahren erfolgreich mit HPA beschichtetes Silizium in die Batterieanode eingebracht, was neben der deutlich erhöhten Energiekapazität auch mit verbesserter Stabilität, Ladefähigkeit und Lebensdauer einhergeht. Die Siliziumpartikel wurden genauso wie die Graphitteilchen mit HPA im Nanometerbereich beschichtet.
Mehr Silizium in der Batterieanode führt zu einer nochmals deutlich erhöhten Energiedichte der Batterie, was die Speicherkosten senkt, also die Batteriekosten pro Ladekapazität reduziert. Silizium hat die Eigenschaft, rund zehnmal mehr Energie speichern zu können als das üblicherweise verwendete Graphit, was es zu einem der vielversprechendsten Anodenmateriale für die zukünftige Entwicklung der Industrie macht. Doch bisher führten spezifische physikalische Eigenschaften von Silizium zu schwerwiegenden ungelösten Problematiken. Erst durch unsere Technologie wird der Einsatz von Silizium in der Anode mit den erwünschten positiven Effekten nutzbar und wirtschaftlich.
Dann erklären Sie doch bitte einmal, wo die Schwierigkeiten in der Nutzung von Silizium als Anodenmaterial liegen.
Silizium ist als Energieträger der Traum der Batterieentwickler. Es ist relativ günstig, belastet die Umwelt signifikant weniger als andere konventionelle Materialien und hat eine 10-fache höhere Energiedichte als das üblicherweise genutzte Graphit. Mit dem Einsatz von Silizium in der Anode ließe sich die Leistungsfähigkeit einer Batterie somit um ein Vielfaches steigern. Das würde beispielsweise die Reichweite von Elektrofahrzeugen beträchtlich steigern, bzw. man käme mit wesentlich weniger Batterien bei gleicher Reichweite aus und die Kosten der E-Autos würden signifikant sinken. Ganz zu schweigen vom Gewicht.
Nun hat aber Silizium einen entscheidenden Nachteil. Mit der Zuführung der Energie dehnen sich die Siliziumpartikel bis zum 3-fachen Volumen auf und bricht bzw. löst sich von der Kupferkontaktfläche. Das bedeutet, der gelöste Anteil steht für den Betrieb der Batterie nicht mehr zur Verfügung. Zudem erhöht sich auf Grund der großen Oberfläche von Silizium der sogenannte Erstladeeffekt, ein Kapazitätsverlust bei dem durch eine Grenzschichtbildung Lithium gebunden wird und nicht mehr für den Batteriebetrieb zur Verfügung steht.
Wenn eine Batterie zum ersten Mal geladen wird, verliert diese auf Anhieb 8 bis 10 Prozent an Leistung. Das passiert, weil die Lithium-Ionen sozusagen an der Anode kleben bleiben und dann nicht mehr für den Energietransfer zwischen Kathode und Anode zur Verfügung stehen. Mischt man nun Silizium hinzu, schnellt dieser Erstladeverlust auf über 30 Prozent hoch. Gleichzeitig geht durch kontinuierliches Ablösen und Neubildung dieser Grenzschicht weiteres Lithium verloren, was die Lebensdauer der Batterie stark reduziert. Somit verpufft der gewünschte positive Effekt der Siliziumnutzung bei herkömmlichen Herstellungsverfahren. Wir gehen nach dem Stand der heutigen Versuche davon aus, das mit der Altech Beschichtungstechnologie diese negativen Effekte verhindert werden.
Wie konnten Sie diese technischen Schwierigkeiten lösen?
Mit unserer Beschichtungstechnologie konnten wir eine Hochleistungs-Silizium-Graphit-Verbundanode entwickeln. Dazu beschichten wir das gesamte Anodenmaterial der Batterie, was aus einem Gemisch aus Graphit und Silizium besteht, mit HPA. Die Lithium-Ionen der Batterie bleiben nicht mehr beim Erstladen „kleben“, das Silizium bricht nicht mehr und auch der Lithiumverlust durch Neubildung von Grenzschichten kann verhindert werden. Sowohl das Aufquellen als auch der Kapazitätsverlust können somit verhindert werden und traten in unseren Labortests nicht auf. Auch konnten wir über eine Testspanne von mehr als 200 Zyklen eine sehr gute Stabilität erreichen. Der Erstladeverlust wurde durch die Technik nahezu vollständig vermieden. In Summe rückt so eine Lithium-Ionen-Batterie mit 30 Prozent höherer Energiekapazität in Sichtweite. Für uns ist das aber nicht das Ende der Fahnenstange. Wir werden nun versuchen, den Siliziumanteil weiter Schritt für Schritt zu erhöhen, was die Leistungsfähigkeit der Batterie noch höher treiben sollte.
In unserem letzten Interview wollten Sie noch keine Zeitpunkte für Ihre Produkteinführung nennen. Wie steht es nun um Ihre Produktion?
Auch hier sind wir einen wichtigen Schritt weiter. Die guten Laborergebnisse haben uns darin bestärkt, den weiteren Prozess hin zu einer ersten Testproduktion und dem Bau eines Fertigungswerks zu forcieren. Entgegen unserer bisherigen Planung hat unser Joint-Venture, die Altech Industries Germany GmbH, an der wir 25 Prozent und die Altech Chemicals Limited, an der wir 75 Prozent halten, deshalb den geplanten Kauf des Grundstücks in Schwarze Pumpe für die Fertigungsanlage vorgezogen.
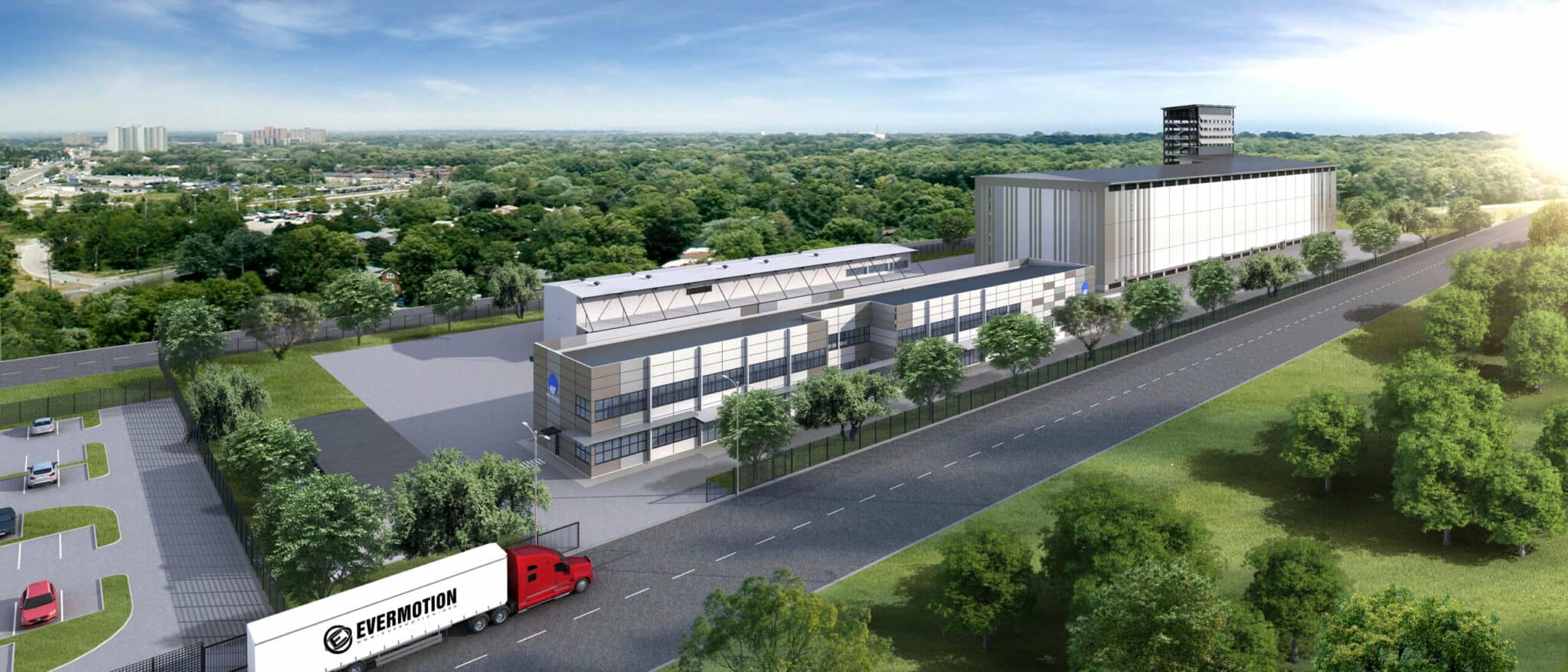
Im nächsten Schritt ziehen wir nun in den bereits angemieteten Räumlichkeiten neben diesem Grundstück zügig die Anlagen zur Produktion erster Testchargen des Anodenmaterials hoch. Ende des Jahres planen wir dann das erste Material zu produzieren und dieses den europäischen Batterieherstellern für Verifikationstests zur Verfügung zu stellen. Wir erwarten, dass wir im 3-Schicht Testbetrieb eine Produktionskapazität von einigen 100 Kilo im Monat erreichen können um ausreichend Testmetrial für unsere potentiellen Kunden zur Verfügung stellen zu können. Parallel dazu werden dann die ersten Schritte für die Planung und den Bau des Produktionswerks eingeleitet.
Das geplante Werk benötigt ja auch die entsprechenden Rohstoffe. Ist die Versorgung für die entsprechenden Batteriematerialien gesichert?
Ja, wir haben bereits heute die Rohstoffversorgung des Werks langfristig abgesichert. Dazu wurden entsprechende Absichtserklärungen zum einen mit SGL Carbon für die Lieferung von Graphit sowie mit Ferroglobe Innovation, einem der führenden Anbieter für metallurgisches Silizium, unterzeichnet.
Sie sprachen bereits das Thema Nachhaltigkeit an und die Vorteile für die Automobilindustrie. Wie gehen Sie mit dem Thema um?
Im Rahmen der vorläufigen Machbarkeitsstudie für die geplante Beschichtungsanlage in Schwarze Pumpe, Sachsen, wurde eine Umweltverträglichkeitsprüfung und eine detaillierte Bewertung des CO2-Abdrucks der Produktionskapazität von 10.000 Tonnen Batteriematerialien pro Jahr durchgeführt. Das entspricht der Kapazität des geplanten Werks.
Das Werk wurde in Übereinstimmung mit geltenden Umweltstandards so geplant, dass Umweltauswirkungen minimiert werden. Die Konstruktion und der Betrieb des Werks werden zu 100 Prozent unter Verwendung von Ökostrom stattfinden. Durch Recycling der Prozessmedien sowie responsible sourcing und kurze Lieferwege wird der CO2-Abdruck der Fertigung signifikant reduziert, im Vergleich zu einer konventionellen Produktion. Das Centre of International Climate and Environmental Research (CICERO) hat das geplante Werk als „Medium Green“ eingestuft. Es stehe mit allen Green-Bond-Prinzipien im Einklang und verursache nahezu keine Scope-1- und Scope-2-Emissionen.
Außerdem reduzieren wir die Emissionen in der Lieferkette dadurch, dass wir ausschließlich mit europäischen Lieferanten zusammenarbeiten.
Noch wichtiger als der Fußabdruck des Werks ist der Effekt auf die Batterieindustrie: Die Studie im Rahmen der Umweltverträglichkeitsprüfung hat ergeben, dass beschichtetes Silizium als Anodenmaterial die CO2-Emissionen von Batterien um ca. 19 Prozent reduzieren könnte, wenn 5 Prozent beschichtetes Silizium in einer Batterieanode verwendet wird. Bei 20 Prozent Siliziumanteil steigt die Einsparung des Treibhausgases sogar auf ca. 52 Prozent, was einer Revolution gleichkommt. Dies wird ein zusätzlicher wichtiger Grund für unsere zukünftigen Kunden sein sich für Altech zu entscheiden.
Nun werden Sie nicht das einzige Unternehmen sein, dass an einer Batterieverbesserung arbeitet. Was macht Sie so optimistisch, dass Altech hier einen Vorsprung hat?
Gerade der Erstladeverlust ist ein schon lange bekanntes Problem der Industrie. Dass eine Ummantelung des Anodenmaterials mit HPA Abhilfe schaffen kann, ist auch wissenschaftlich anerkannt. Die Herausforderung besteht darin, nicht nur im Labor das HPA sehr gleichmäßig und hauchdünn aufzutragen, sondern in einem industriellen Prozess. Gelingt das nicht, tritt der gewünschte positive Effekt nicht ein. Das von uns entwickelte nasschemische Verfahren ermöglicht einen günstigen und zuverlässigen Weg, um Aluminiumoxid gleichmäßig und hauchdünn auf das Anodenmaterial aufzubringen. Unsere Technik ist im Gegensatz zur Konkurrenz skalierbar, rentabel und entspricht der benötigten Qualität in der Beschichtung. Der erwünschte Effekt der Leistungssteigerung tritt ein und kann von uns in einen industriellen Prozess überführt werden. Ein Patentantrag zum Schutz der Beschichtungsmethode wurde bereits gestellt.
Gibt es bereits konkrete Anfragen aus der Autoindustrie?
Natürlich wird sehr genau beobachtet, was wir tun. Erste Anfragen gab es bereits aus dem Markt. Doch bisher halten wir uns noch etwas bedeckt. Wir werden erst unser Testmaterial produzieren und damit die entsprechenden Batteriehersteller beziehungsweise Autoproduzenten überzeugen. Wichtig ist es nun erst einmal das Testmaterial zu produzieren und zur Verfügung zu stellen. Das soll Ende des Jahres geschehen. Dann werden die weiteren Gespräche beginnen.
Mit welcher Nachfrage rechnen Sie mittelfristig?
Der Batteriemarkt, alleine in Europa, ist gigantisch. Hierfür halten wir auch die entsprechenden Lizenzen. Wenn Sie mal auf die bestehenden und geplanten Gigafactories schauen, sehen Sie sehr gut, was da gerade entsteht. Folgt man den Zahlen von McKinsey werden bis 2040 jährliche Kapazitäten von 0,7 bis 1,5 Terrawatt entstehen. Die Nachfrage nach hoch qualitativem und möglichst effizientem Anodenmaterial wird nicht das Problem sein, sondern vielmehr das Angebot. Es scheint so, dass wir genau zum richtigen Zeitpunkt mit dem richtigen Produkt an den Start gehen werden.
Sie haben nun auch vorläufige Zahlen für das Geschäftsjahr 2021 veröffentlicht. Führen Sie uns kurz durch die wichtigsten Kennzahlen.
Die AAM wies nach vorläufigen Zahlen im Geschäftsjahr 2021 einen voraussichtlichen Verlust in Höhe von 874.000 Euro aus. Im Jahr zuvor lag der Verlust bei 618.000 Euro. Tatsächlich haben wir um 26.000 Euro besser abgeschlossen als geplant. Die vorläufige Bilanz zum 31. Dezember 2021 nach HGB weist ein Eigenkapital in Höhe von 3,166 Millionen Euro aus. Bedingt durch die durchgeführte Kapitalmaßnahme im Sommer haben wir fast 2,2 Millionen Euro mehr in der Kasse als im Jahr zuvor. Das ist auch gut so, denn wir wollen nun zügig unser Testwerk errichten und die ersten Chargen des Anodenmaterials produzieren.
Wann ist der Break-even zu erwarten?
Wir sind noch in der Investitionsphase. Auch dieses Jahr werden wir keine positiven Erträge haben und weitere Verluste generieren. Das ist aber in dieser vorindustriellen Aufbauphase nicht ungewöhnlich. Wir müssen faktisch zwei Werke aufbauen. Sobald wir dann in der Produktion sind, werden die entsprechenden Umsätze generiert. Das wird aber sicherlich noch etwas dauern.
Das heißt aber auch, dass Sie noch Kapitalbedarf haben. Wo soll das frische Geld herkommen?
Mit der bereits genannten Zertifizierung von Cicero sind wir jetzt „Green-Bond-fähig“. Das bedeutet, dass wir für Anleger, die in zukunftsweisende und nachhaltige Unternehmen wie unseres investieren wollen, die nötigen Voraussetzungen erfüllen. Das kann in Zukunft für uns ein attraktiver Weg sein, spannende Investorengruppen in ganz Europa über eine entsprechende Grüne Anleihe anzusprechen. Weitere Kapitalmaßnahmen wollen wir ebenfalls nicht ausschließen. Dazu steht uns natürlich auch noch die Finanzierung über Fremdkapital als weitere Option zur Verfügung. Als nächsten großen Schritt haben wir den Aufbau des Testwerks gemeinsam mit unserem Partner Altech Chemicals Limited in der Altech Industries Germany GmbH geplant. Mit Abarbeitung dieses nächsten großen Meilensteins werden wir unter Beweis stellen, dass wir über das Wissen und die Technik verfügen, richtungsweisendes Anodenmaterial für die Energiewende der Batterieindustrie und für die Automobilhersteller zur Verfügung zu stellen.
Herr Ahrens, vielen Dank für das Interview!
Dipl.-Wirtsch.Ing. Uwe Ahrens | Vorstand Altech Advanced Materials AG
Herr Uwe Ahrens ist erfahrener Industriemanager der Melewar Industrial Group und Geschäftsführer der MIE TECH Sdn Bhd. Herr Ahrens ist Dipl. Wirtsch.-Ing. (MB) mit Abschluss von der Technischen Universität Darmstadt, Deutschland. Nach seinem Abschluss trat Herr Ahrens in den internationalen Maschinen- und Anlagenbauer KOCH Transporttechnik GmbH in Deutschland ein, der heute zur FLSmidth Group gehört, wo er 12 Jahre lang in leitender Funktion tätig war, hauptsächlich in Deutschland, den USA und Südostasien.
Kurzinfo zum Unternehmen
Altech Advanced Materials AG (ISIN: DE000A2LQUJ6), Frankfurt, ist eine an der Frankfurter Börse notierte Beteiligungsgesellschaft. Ziel der Gesellschaft ist es, am Markt für Lithium-Ionen-Batterien und damit am stark wachsenden Sektor der Elektromobilität sowie an der erwarteten Marktentwicklung für die weiteren Anwendungsgebiete von hochreinem Aluminiumoxid zu partizipieren. Zu diesem Zweck hat sich die Altech Advanced Material AG mit 25 % an der Altech Industries Germany, Dresden, („AIG“) beteiligt, wo gemeinsam mit dem Partner Altech Chemicals Limited, Australien („ATC“) eine Fabrik zur Herstellung von Beschichtungsmaterial für Batterie-Anoden geplant ist.
Aktuell im nwm: